The operation of automotive batteries is associated with increased loads due to significant temperature fluctuations in the engine compartment, exposure to dirt, dust and moisture. In addition, sometimes situations arise associated with overheating of the battery and the release of excess pressure through the valves with the release of acid vapor.
All this inevitably leads to a gradual deterioration of contact and oxidation at the terminals. To reduce the negative oxidizing effect of various reagents on the contact pads of the battery, lubricants are used that spread on top of well-assembled joints.
Content
Is it always necessary to protect the terminals from oxidation
In a technically sound car with a good battery, which does not have cracks in the body, including those caused by excessive efforts when twisting the terminals, their oxidation occurs very slowly. If the car is parked in a dry and ventilated place, the risk of contact deterioration is further reduced.
Nevertheless, no matter what ideal conditions the car is used in, oxidation and burning of contacts inevitably occur in it, which is most pronounced at the battery terminals, where huge currents of hundreds of amperes pass at the time of starting the starter. In addition, water vapor and oxygen are always present in the air, which slowly but surely lead to corrosion of metals.
If there is a whitish coating that most often occurs on the positive terminal of the battery, the use of protective grease makes it possible to continue using the car if it is not possible to replace the battery. To do this, it is necessary to clean the contacts, put the felt pads soaked with grease between the battery case and the terminals, connect them to the conductors, tighten and grease the contact connection from above. The negative terminal also needs protection from burnout and oxidation, due to the constant presence in the engine compartment with hot dust and moisture in the engine compartment.
The use of grease for the terminals will help extend the life of the battery and improve the overall reliability of the car. The use of special compounds to protect the battery terminals seems to be a reasonable preventative measure, able to reduce the number of unpleasant surprises that may appear at the most inopportune moment.
How to lubricate the terminals against oxidation
The main purpose of lubricating electrical connections is to prevent dirt and oxygen from entering the contact area, which helps to prevent oxidation.
It is desirable that the protective coating does not collect excess dirt and perform its protective functions as long as possible. There are many different options for protecting battery terminals, each of which has certain advantages and disadvantages. The main condition should be the absence of a corrosive effect on the contacts, the insulation of the wires and the surrounding rubber parts, high temperature and acid resistance.
Graphite grease
These are compositions, usually based on mineral oil with the addition of graphite powder. They have good water repellent properties and excellent corrosion protection. A conventional graphite lubricant can withstand temperatures from -20 to +70 degrees, but there are also more expensive high-temperature options. In connection with the possible overheating of the engine compartment in hot weather, it is better to use them.
Graphite conducts electric current well, so its penetration into the contact joint does not worsen the electrical contact as much as a grease with dielectric properties does.
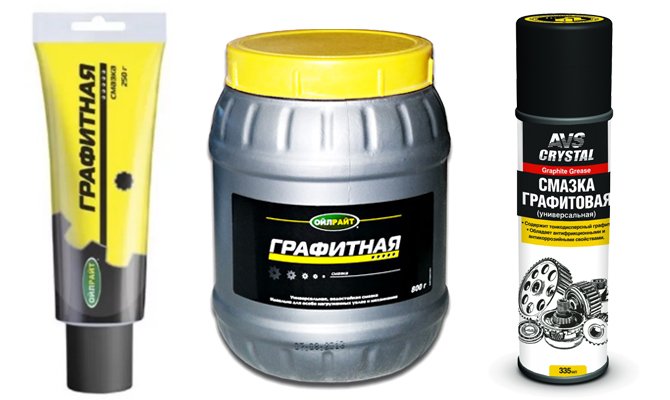
Grease
This type of grease withstands high temperatures, has anti-corrosion properties, holds well on the surface, but does not conduct electricity. They are made on an oil basis with the addition of special additives and dyes, which facilitate the application of a protective coating.
This is a good option for protection against oxidation when using special formulations for protection, for example, from LiquiMoly, Addinol, Molykote, Gunk and others.
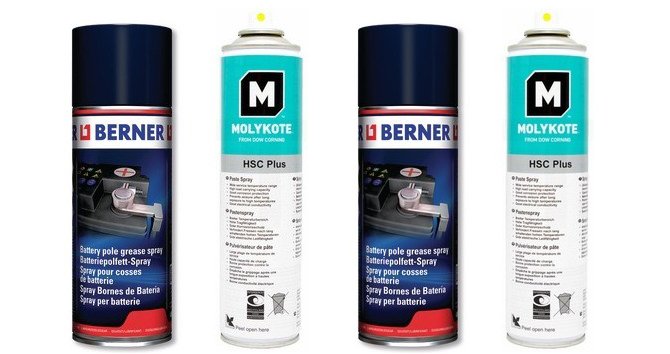
Copper grease
These greases are durable, have a high viscosity, conduct electricity well, withstand high temperatures (from -35 to several hundred degrees), perfectly protect against corrosion, moisture, burnouts.
Special copper greases are available for electrical contacts in the form of sprays, for example, Berner, as well as copper smears for highly loaded moving joints. They have different properties, but both options can be used to protect battery contacts.
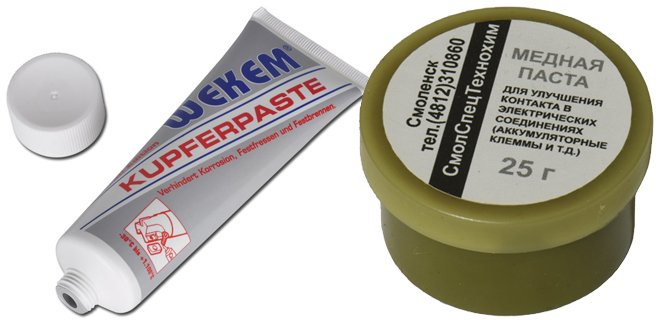
Wax based greases
These greases withstand temperatures from -30 to +130 degrees, have an average viscosity, hold well on the surface and provide high tightness of electrical contacts.
A good wax-based compound is Presto Batterie Pol Schutz, which can withstand temperatures from -30 to +130 degrees and is easy to apply with an aerosol spray.
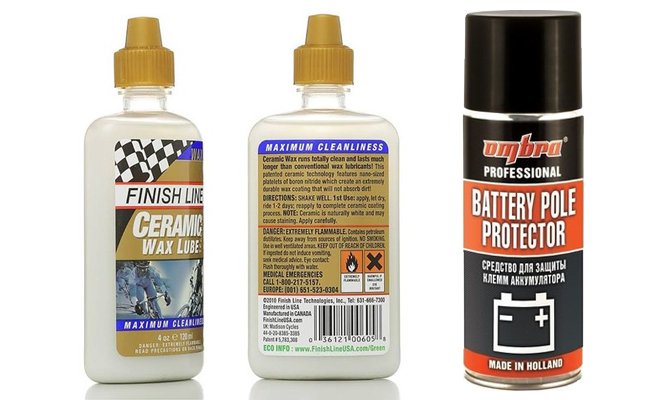
Silicone grease
This is an excellent option for protecting contact compounds with good resistance to hot vapors, disinfectant solutions. Silicone grease adheres to surfaces perfectly, is neutral and is able to work in a wide temperature range from -40 to +150 degrees. It is produced by many trusted manufacturers, including Shell, Fuchs, Molykote, Roco and others.
The disadvantage of silicone greases is the need for regular updating of the protective coating.
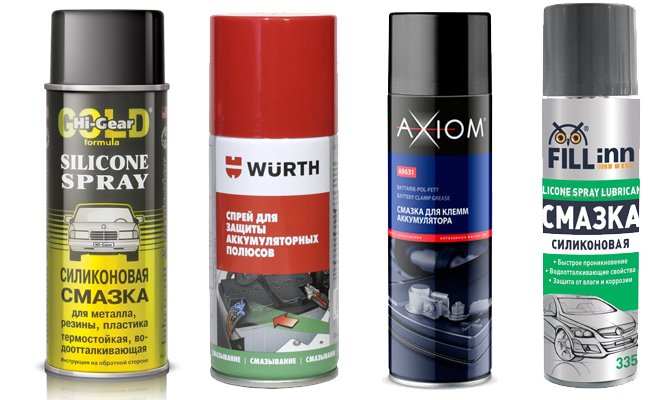
Oil Based Compounds
These include such common formulations as solidol, lithol, cyatim 201, petroleum jelly. These compounds are used to protect against wear of rubbing surfaces, have high fluidity, which increases with increasing temperature in the engine compartment, so they are not very suitable for protecting electrical contacts. If there are serious problems with the oxidation of the contacts, they can be used to protect the terminals, but it is better to do this only in the winter season, when these greases are less fluid.
There are special formulations based on mineral oils containing special additives that improve their temperature resistance and therefore make it possible to use them to protect the terminals. These include:
- Liqui Moly Kupfer Spray is a copper powder oil lubricant for brake pads. It can also be used as a protective coating for the outer surface of the contacts;
- Liqui Moly Batterie Pol Fett is a special protective grease with a red dye. Permissible temperatures are from -40 to +60 degrees.
- Vmpauto MC1710 - a mixture of various oils, as well as silicone with a blue dye. It can be used at temperatures from -10 to +80 degrees.
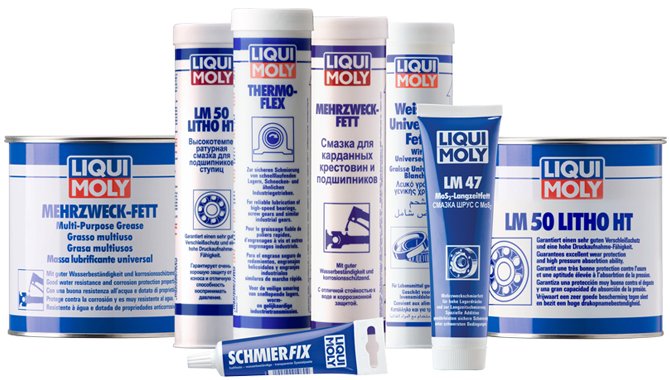
Teflon grease
These greases are designed to form a dry coating on the rubbing parts. They are not well suited for protecting electrical contacts due to their high penetration ability, which can degrade electrical contact.
Disruption of contact in the battery terminals, where very strong currents flow, is not only undesirable, but also a dangerous phenomenon. In this regard, it is not recommended to use Teflon lubricants on contact joints.
How to lubricate the terminals
The protective properties of the lubricant are exerted only with good and good electrical contacts in the protected connections. If it is not there, then applying grease will not restore it.
When applying grease to the terminals, you need to understand that between the contact surfaces it does not need to be applied, so as not to impair the conductivity. Before connecting the terminals to the conductors, it is necessary to achieve the perfect purity of the metal on the contacts, up to processing with a rough cloth or fine sandpaper, wipe them with alcohol, and only then twist. After this, it is necessary to apply a protective composition to the compound assembled and tightened with the necessary force. If the lubricant is thick, then it can be greased with a rubber glove, and when using a spray, treat the protected surfaces from a spray can.
The application of conductive copper grease inside the contact pads can be justified in case of their poor quality, the presence of large irregularities that reduce the total contact area.
Attention! If dielectric grease gets into the space between the battery contacts with the wiring of the car, this will worsen the conductivity of the contact and, if the current is high, it will cause a burnout, further worsen the conductivity, as well as the risk of melting of the insulation of the wires and even a fire due to the high temperature.
Precautionary measures
As a rule, all technical lubricants are to one degree or another toxic to the human body. Therefore, work on their application must be carried out with gloves. In case of contact with technical greases, wash them off immediately with warm water and soap.
Important! When applying protective grease, make sure that it does not get on rubber tubes, gaskets and other surfaces that do not need such treatment. This is necessary in order to avoid the destructive effect of the components contained in the lubricants on these materials.